As the semester is approaching an end, all G1 physics students were given a particular task that would draw a meaningful end to the school year – the Mousetrap Car Project. As an iconic STEM contest integrating science, technology, engineering, and mathematics, the project is very popular worldwide. With only a simple mousetrap as the motive power source, students competed to build a mousetrap car that could travel the furthest distance.
Students were divided into groups of 2 to 4 and were challenged to design a well-developed car model. Teamwork and communication played an essential role in the designing process as the project assesses students’ ability to cooperate and discuss with each other through researching, comparing, and giving feedback.
The mechanism of a moving mousetrap car is simple: the torsion spring on the mousetrap is initially twisted beyond its equilibrium position. When the trap closes, the strain energy of the spring converts into kinetic energy. Then, by attaching a string to the mousetrap’s arm and winding it around a shaft, the shaft and the wheel will rotate when the mousetrap lever is loosened and the string is pulled.
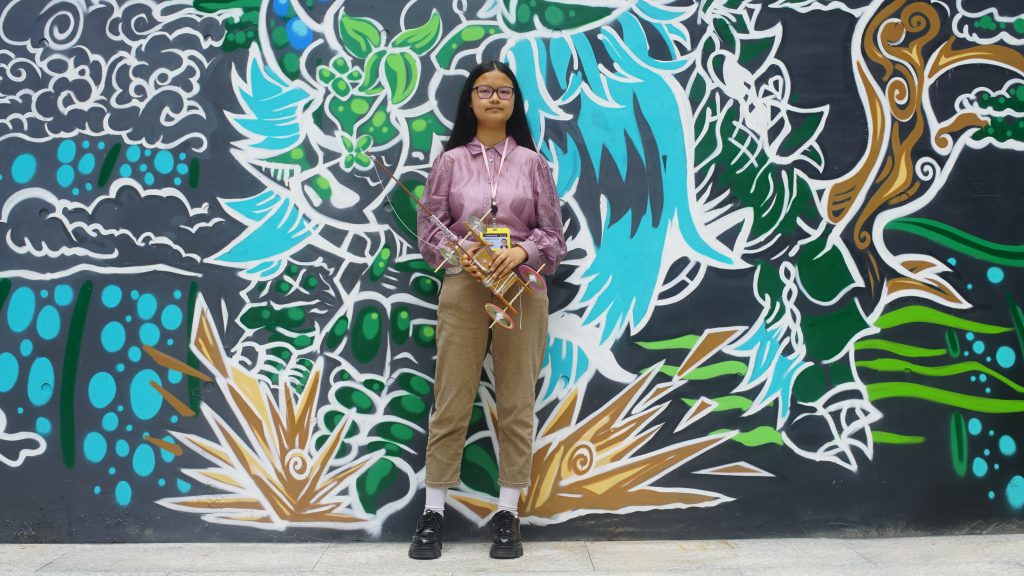
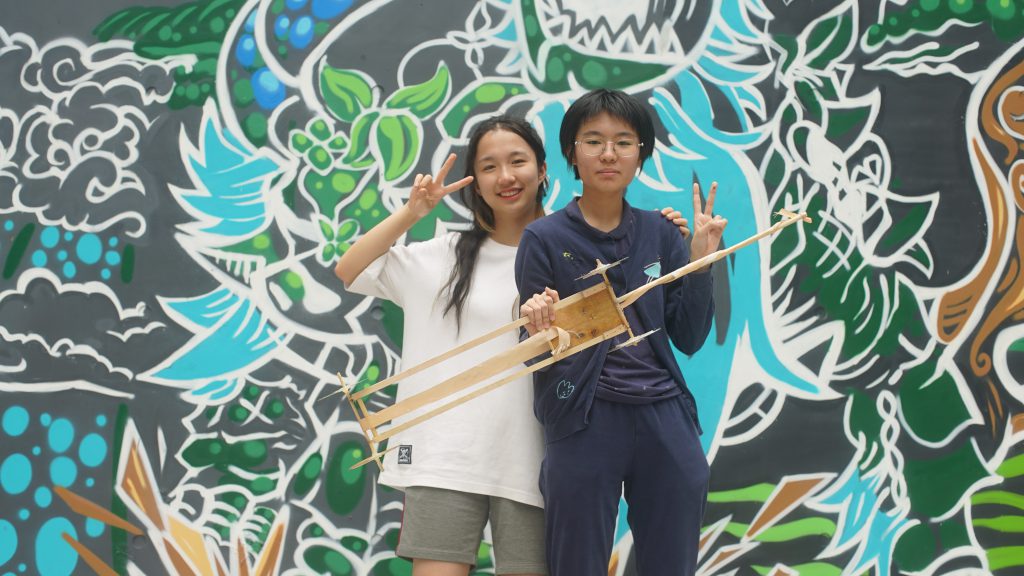
This project gives us a break from the regular learning curriculum and focuses on a more practical side of science. It strengthens our understanding of related physics topics and highlights the infinite possible applications of physics in our life.
As fascinated by design and engineering, I was full of determination after hearing about the upcoming competition and dug right into the researching phase with my team members. We followed the stem engineering process: we asked, imagined, planned, created, tested, and improved to put forward an intricate design.
Four critical factors contribute to a well-crafted long-distance car. First, we wanted to achieve the smallest possible force over the longest distance. By using an axle only 3 mm in diameter but a back wheel that is 350 mm wide, in addition to an extended lever arm, the car gains a strong build-in mechanical advantage in which one complete turn in the axle allows the car to travel a longer distance. Next, our biggest enemy was friction. We installed ball bearings between the axle and the car body to avoid unnecessary energy loss caused by friction. Because the more the car weighs, the more energy is lost from the mousetrap spring; we decided to minimize the car’s weight by using ultra-light balsa wood. In addition, our group further reduced the thickness of the wheels to 1 mm, minimizing the total weight of the car and the rolling friction between the wheels and the ground.
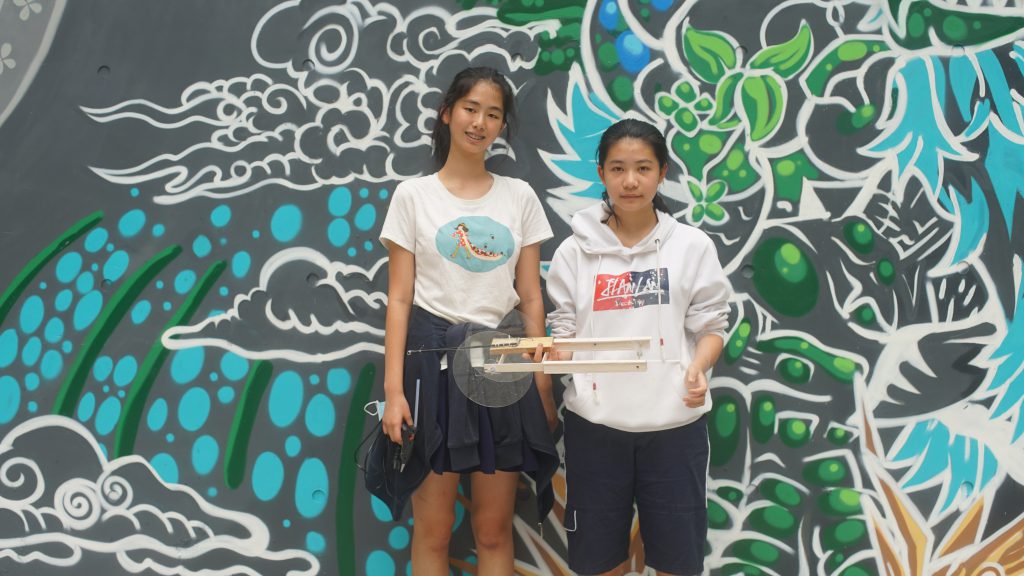
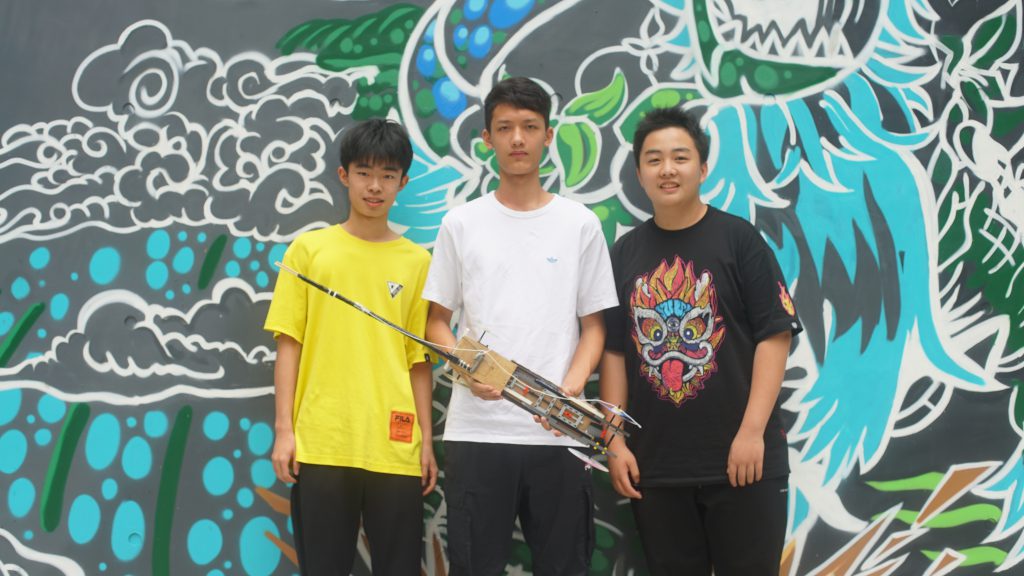
While the project was loaded with challenges, I enjoyed the tweaking and testing process. We took in every little area for improvements and refined our car to give it the best outcome. It took us a tremendous amount of time to take in every detail, but the sense of accomplishment was the driving force for us to reach our goal. Though our group was bombarded with countless difficulties, such as aligning the wheels on a straight line or fixing bearings into the balsa wood, we believed there are always more solutions than problems. Being strangled with problems was stressful, but it was also those moments when we assimilated and learned from our mistakes. For example, when our team realized that the wheels were not aligned correctly and had to dismantle the car body, we understood that a small error could lead to the design imbalance. Likewise, when the glue and the string both didn’t work, we examined and ran trials individually with five types of glue and tapes and four types of ropes and strings to find out which combination would give us the sturdiest structure.
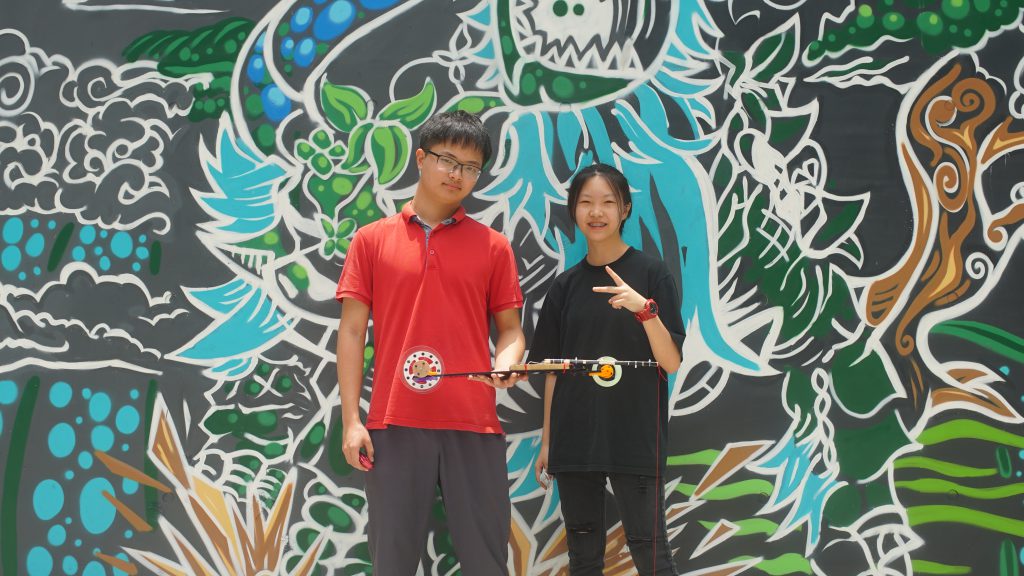
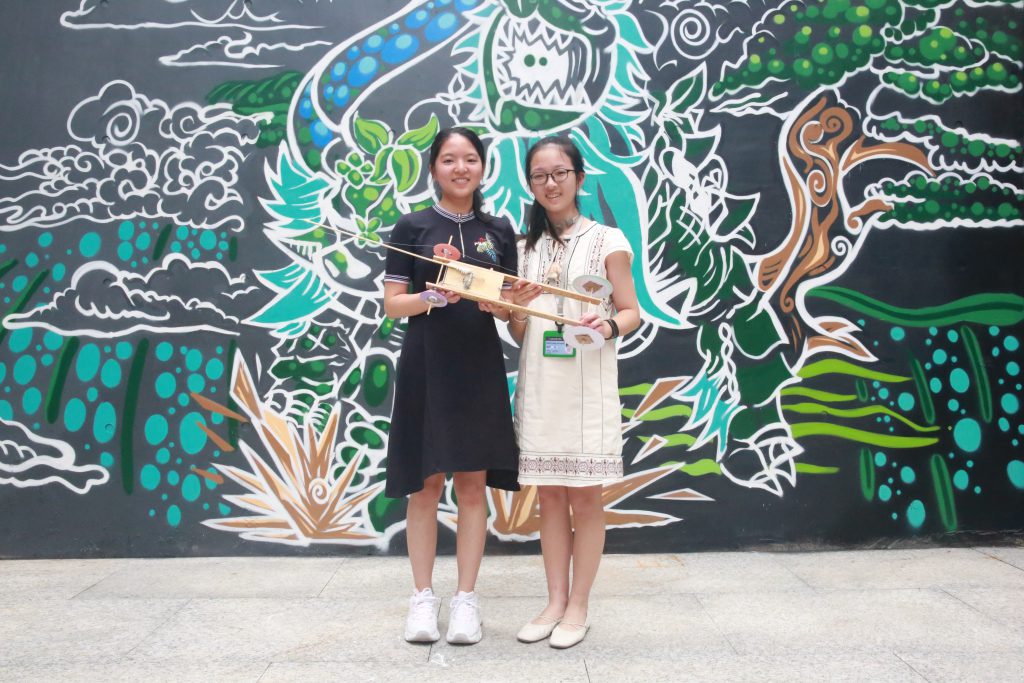
In the project, I learned the necessity of balancing the principles presented in our car. I believe there is no such thing as a perfect car: in gaining other advantages, there will always be some factors to give up. For example, our group saw great results from making our car as light as possible, but the payoff was that balsa wood could be fragile and easily bent; therefore, we needed to make our structure more stable and rigid. Thus, I learned to understand the meaning of optimization-to make full use of a limited situation.
There was stress and pressure, but everything was worth it after getting our results. Challenges elevated our spirits. When our car finally sped down the corridor with confidence and traveled an astounding 54 meters, our worries turned into relief and ecstasy.
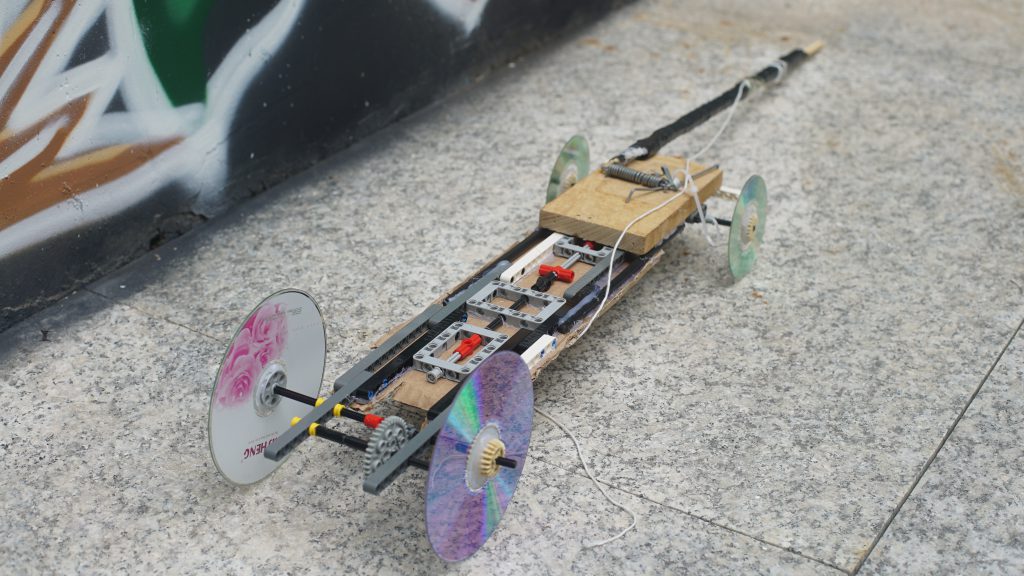
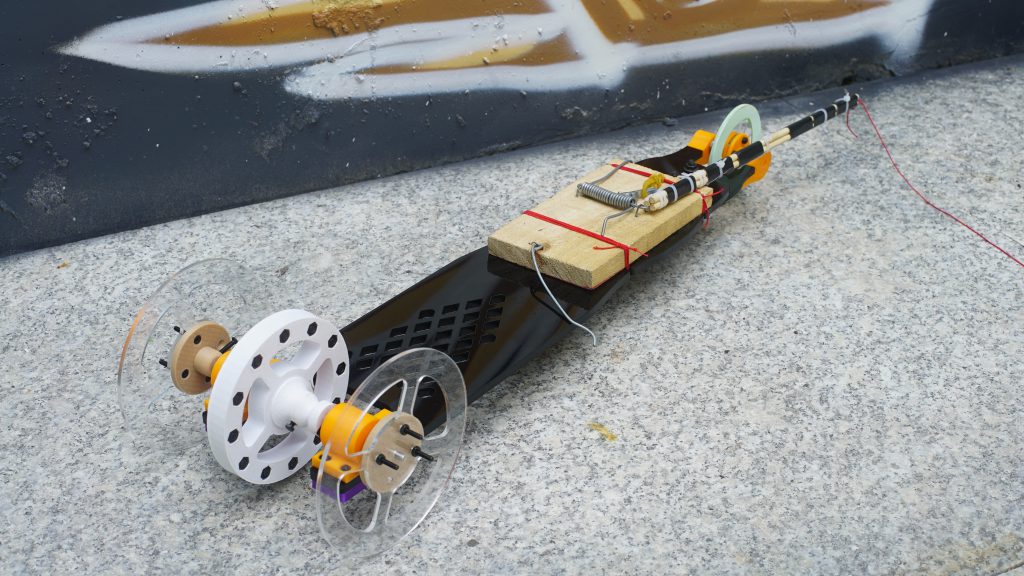
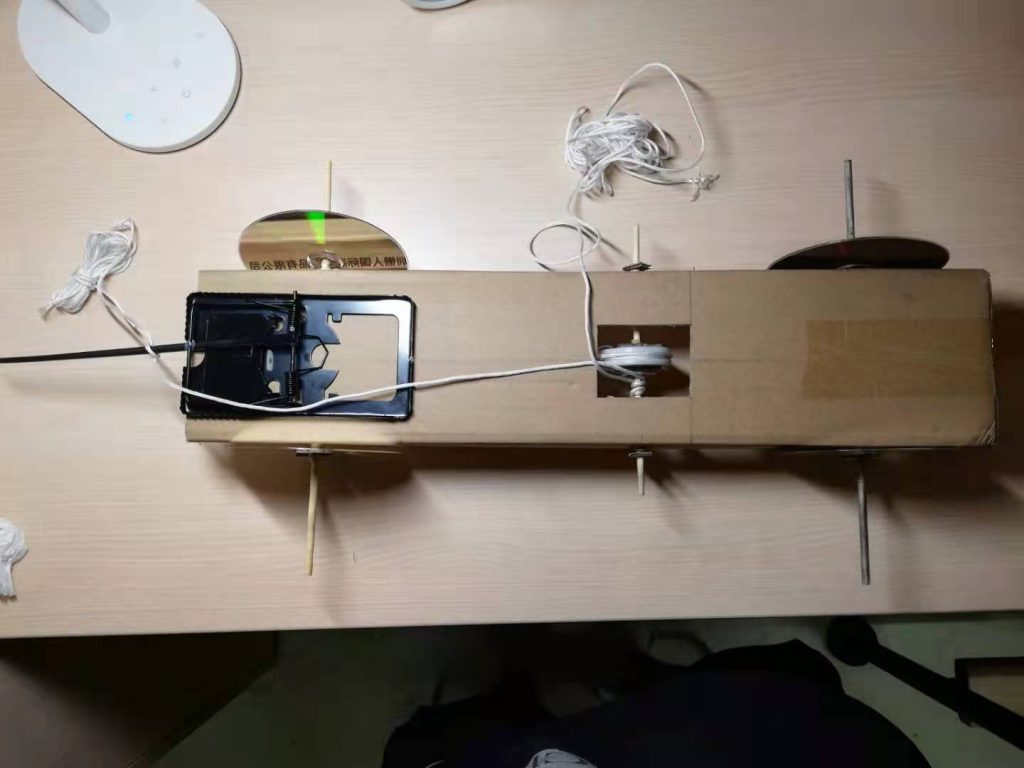
This project helped us cultivate meaningful and useful skills, such as critical thinking, problem-solving, team interactions, and time management. I appreciatedhaving such a valuable experience. This opportunity has enabled me to acquire skills beneficial to my learning career and fruitfully marks the last chapter of the school year.
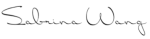
- Article / Sabrina Wang